

People in every walk of life will have reasons to remember 2020 as a year unlike its predecessors, including business owners and managers who navigated uncharted waters in dealing with a deadly virus.
The global spread of COVID-19, the disease caused by the novel coronavirus, was a public health crisis that demanded rapid responses from governments and the private sector. In March and April, simply obtaining “essential industry” status was the first important hurdle recyclers had to clear in the western world.
Processors, consumers and traders of all materials felt the impact of COVID-19 and subsequent restrictions. Volumes and profits in 2020 did not meet the prepandemic expectations of numerous companies. However, considering the path that had to be traveled, most recycling firms can look back and be grateful they managed through a turbulent year.
Less metal, smaller profits
While grappling with one of the biggest economic downturns in U.S. history in the second quarter, metals recyclers had to consider employee layoffs and even idling some locations in the face of material flows that plummeted rapidly.
Despite being in the thick of numerous challenges, the metals recyclers who gathered (online) for the Recycling Today State of the Scrap Recycling Industry Roundtable in May already were expressing confidence that their industry’s resilience would carry it through the turmoil. (For more from Recycling Today’s The State of the Scrap Recycling Industry, visit www.RecyclingToday.com/keyword/soi-scrap.)
Panelist Becky Proler of Houston-based Southern Core Recycling credited the scrap sector’s family business model as a key factor. “I think resilience is probably the best word to use to describe the family business model,” she said.
Proler continued, “It’s been resilient for over 100 years, and these third and fourth generations—I think somebody said it very well—we’ve seen everything. Family businesses know how to be flexible. They know how to operate in good times and bad times, and I think this is just part of the curve.”
The curve thrown by COVID-19 turned out to be substantial and was showing its own resilience in November in the U.S. with a growing wave of new cases that surpassed levels reported in March and April.
In the ferrous sector, scrap-fed electric arc furnace (EAF) steelmakers such as Nucor Corp. and Steel Dynamics Inc. saw their earnings scaled back compared with 2019, but they remained profitable. Nucor earned more than $320 million in net income in the first three quarters of 2020.
Portland, Oregon-based publicly traded scrap firm Schnitzer Steel Industries, which had a fiscal year that ended Aug. 31, reported an annual net loss of $4 million, though it claimed an operating income of $27 million. (More on the ferrous scrap sector can be found in the article “Avoiding the worst,” starting on page 36 of the print edition.)
The narrower profit picture reflected a year where scrap volumes were restricted and operating expenses rose tied to distancing measures; but, just enough profit remained thanks to sufficient demand for ferrous and nonferrous scrap.
In the nonferrous sector, aluminum demand was hit hard by the shutdown in automotive and aircraft manufacturing that occurred in the early spring. While automotive manufacturing resumed in mid-May, aircraft manufacturing has yet to bounce back significantly in light of the pandemic’s impact on air travel. However, this reduced demand was met by reduced retail and industrial scrap generation. Sources Recycling Today talked to in April and May said their volumes of incoming scrap were down as much as 50 percent.
As of October, aluminum was gaining strength, with a processor in the Upper Midwest saying secondary aluminum scrap grades had increased in pricing relative to some primary grades.
In the red metals sector, a processor based in the Midwest told Recycling Today in mid-July that while generation had improved, it remained softer than normal for that time of year. “The higher market has helped things,” he said, referencing the COMEX settlement price, which was then in the $2.90 per pound range.
Copper scrap was in short supply at that time, with the processor saying, “We’re all going after the same material. There is a squeeze on material and on margins. Margins are out the window in favor of finding material to satisfy consumer needs.”
As of October, that was no longer the case. A processor and trader whose company has operations in the Southeast and Upper Midwest told Recycling Today that it seemed as if every copper consumer had a planned or unplanned outage scheduled as of mid-October or that they were drawing down inventories with the end of the year approaching.
As the resurgence of COVID-19 in November demonstrated, the challenges of the new decade are likely far from over, a circumstance touched upon at the Recycling Today roundtable by Ben Abrams of Pennsylvania-based Consolidated Scrap Resources.
“I think the next couple of years are going to be tough, and this period that we’re in now of somewhat stable pricing is the result [of] weaker scrap flows,” he said. “It’s going to change as the United States economy and global economies try to get back into a rhythm and some growth. That’s a big unknown, so you have to figure out what works for you and go forth and do that. But I think we’re going to have some challenging economic times over the next few years before it gets good again.”
Demand for fiber endures
Steady demand paired with reduced flows characterized the market for old corrugated containers (OCC) and other recovered paper grades in the first half of the year. While idled automobile assembly plants and demolition sites affected scrap metal flows to processing yards, at material recovery facilities (MRFs) deciding how to safely collect and sort household recyclables put the pinch on scrap paper supplies in late March and April.
In the early weeks of the pandemic in the U.S., public health officials were trying to determine to what extent the virus spread because of surface contact versus airborne transmission. Safety initially dictated a halt in many sorting operations until workforce protection measures could be put in place at MRFs and other recycling plants.
As sorted scrap paper supplies were dropping, demand for finished containerboard and tissue was staying put or rising, causing an inevitable spike in prices. “I’ve never seen generation as off as it is now,” a recycler in the mid-Atlantic region told Recycling Today in early May.
He added, “In some areas of business, we’re seeing increases, like in grocery, but then the entire retail sector is dead. With office paper, generation is only 30 to 40 percent what it was. Generation has been drastically down. Overall, we could see paper prices continue to remain high until COVID-19 goes away.”
In the second half of the year, supply began catching back up with demand, causing recovered fiber prices to drop in June and July and stabilize thereafter. This also brought forward the major nonpandemic-related factor in the global scrap paper market: The closing door to the People’s Republic of China.
With a Jan. 1, 2021, ban on scrap paper imports by China looming, Dan Gee of Recovered Paper Consulting LLC and Atlanta-based Moore & Associates said in mid-October, “Shipments to China are rapidly winding down.”
Throughout 2020, that nation’s government had issued fluctuating quotas allowing some grades (mostly No. 12 OCC) to enter China’s ports. As those quotas played out heading closer to 2021, brokers told Recycling Today the “double-sorted” OCC No. 12 grade that formerly headed to China was likely sailing off into an uncertain future with fewer global buyers.
Despite the ongoing hunger for recovered fiber at Chinese mills, the nation’s government has thus far reclassified some nonferrous grades from “waste” to an allowable imported “resource” and has published specifications to do the same for ferrous scrap before it reconsiders paper grades. Even plastic scrap reportedly is ahead of scrap paper with Chinese regulators who have made moves to allow recycled-content plastic pellet imports.
For North American MRF operators and other recyclers of paper and plastic, investments in domestic paperboard output and plastic scrap reprocessing capacity have been bright spots amid China’s closing ports and the COVID-19 economic turmoil.
In the paper and board sector, mill conversions from printing and writing grades to packaging grades remained a trend in 2020. ND Paper LLC, the U.S. subsidiary of Hong Kong-based Nine Dragons LLC, is converting a mill it owns in Maine to produce packaging grades; Canada-based Cascades is doing the same at a mill in Virginia; and Canada-based Domtar is converting a paper machine to recycled-content linerboard production at a Tennessee mill.
The investments in plastic reprocessing have been widespread, creating some medium-term optimism in a sector that has needed a boost in domestic markets in the post-China-imports era.
Plastic pioneers seek ROI
During the most robust years of China’s economic growth, the manufacturing sector there imported millions of tons of plastic scrap each year for eventual use in an abundance of finished goods. By 2013, after recyclers and traders in North America had become accustomed to shipping plastic scrap of nearly every variety (including mixed plastics) to China, the nation’s government began reconsidering its open-door policy for the material.
China’s closing door came just as environmental advocates around the world sounded the alarm about discarded plastics’ widespread presence in the environment. Subsequently, producers of plastics and packaging made from the material have had little choice but to begin investing in recycling alternatives.
In the European Union and some other nations, these investments have been encouraged by mandates and (sometimes) increased funding. In North America, the government intervention has been less frequent, but investments are underway.
No. 1, polyethylene terephthalate (PET), bottles have received much of the attention, with companies like Los Angeles-based CarbonLite investing in bottle-to-bottle capacity, with longtime buyers such as Georgia-based Mohawk Industries and Ohio-based Evergreen Plastics among the companies investing to expand or maintain their PET reprocessing capacity.
But if the global plastic recycling rate is to move upward (estimated by some groups as at less than 10 percent), investments in a wider variety of discarded plastics is necessary.
Orlando, Florida-based PureCycle Technologies says it completed bond financing in 2020 required to build a commercial-scale recycling plant for polypropylene (PP) scrap in Ironton, Ohio.
That company’s CEO says PureCycle’s solvent-based technology was originally developed by Procter & Gamble. He says that consumer goods company uses PP packaging more than that of any other resin and that the firm remains interested in the progress of the PureCycle project.
Some of the announced investments in the plastics recycling space this year involved processes categorized as advanced or chemical recycling. Among these ventures, which break discarded materials down to monomers or convert them to fuels or chemicals, is an announced polystyrene (PS) chemical recycling facility to be built in northern Illinois.
A September report by several advocacy groups, including the Basel Action Network (BAN), Break Free From Plastic, Greenpeace and Rethink Plastic, lists more than 50 advanced or chemical recycling projects and attempts to rate their operational status. The majority of the projects were listed by the groups as “questionable” or “difficult to evaluate” based on a lack of current information. Only about a dozen of the projects were found by the groups to be fully operational, with several others rated as likely to be operational at some capacity.
The advocacy groups acknowledge their preference for closed-loop (i.e. bottle-to-bottle) recycling versus the newer conversion processes. However, such skepticism likely was boosted after an October article on an investment short-selling website questioned the science behind the plastic conversion technology of Canada-based Loop Industries.
Nonetheless, plastics trade associations appear to remain committed to the notion that landfill diversion of plastics, particulary those deemed hard to recycle, will involve technologies beyond what has come to be known as mechanical recycling. As practitioners of the traditional form of plastic recycling enter 2021, they will be watching as closely as anyone whether “advanced recycling” will lead to measurable advances in the amount of plastic profitably recycled.
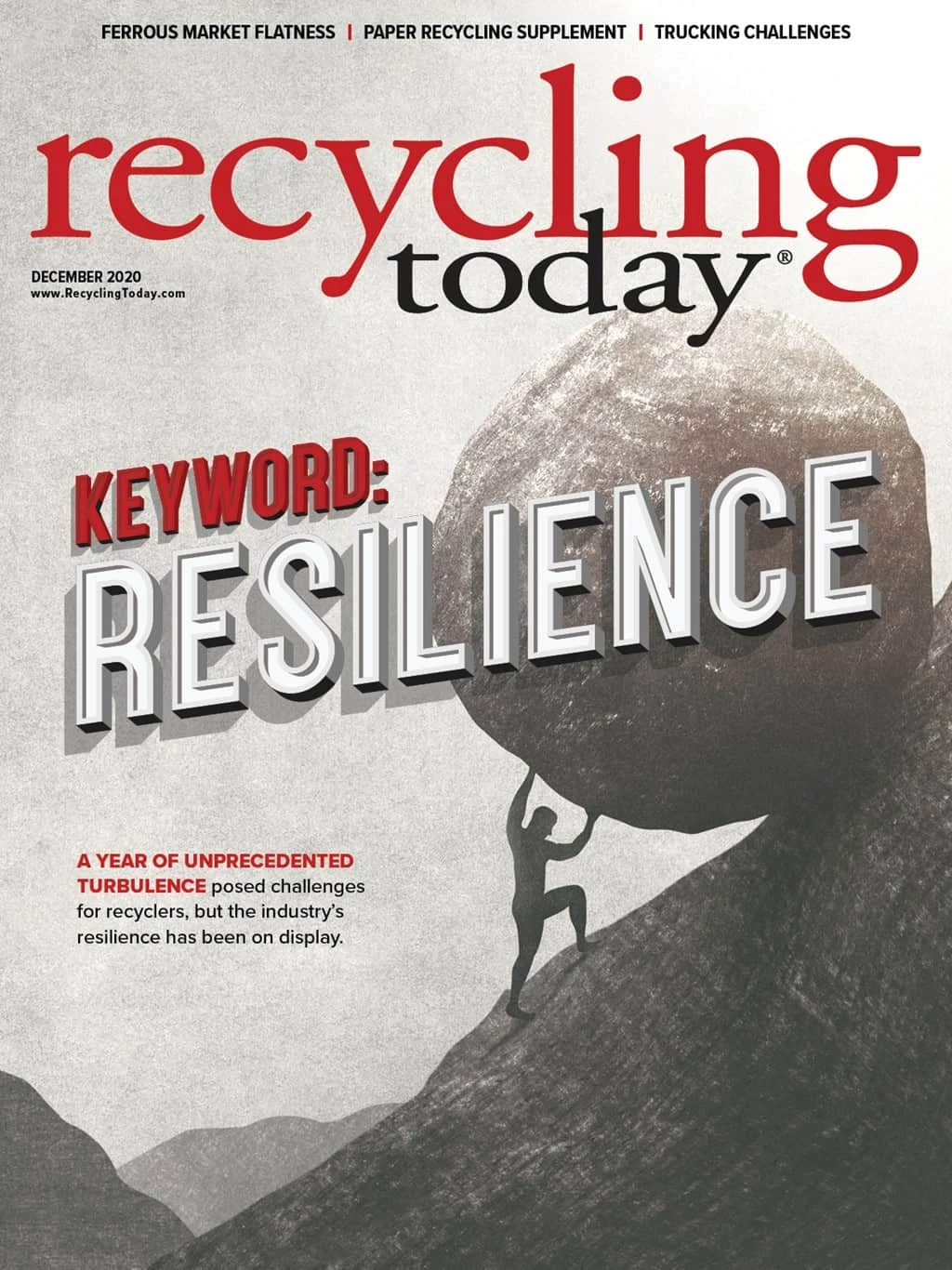
Explore the December 2020 Issue
Check out more from this issue and find your next story to read.
Latest from Recycling Today
- Aqua Metals secures $1.5M loan, reports operational strides
- AF&PA urges veto of NY bill
- Aluminum Association includes recycling among 2025 policy priorities
- AISI applauds waterways spending bill
- Lux Research questions hydrogen’s transportation role
- Sonoco selling thermoformed, flexible packaging business to Toppan for $1.8B
- ReMA offers Superfund informational reports
- Hyster-Yale commits to US production